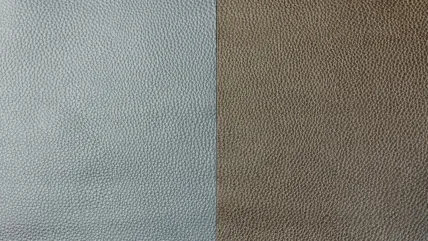
Representing the first stage in the leather-making process, the beamhouse process is crucial. It is here that the rawhide is cleaned and soaked, dehaired and degreased. After which, hides are split into a grain layer, making the leather thinner and more flexible. Hides split in the beamhouse are typically used in the automotive and aviation industries, as well as in interior design.
So, with nearly 70% of all waste water in traditional leather production originating in the beamhouse, the benefits of 100% sustainable, non-hazardous chemicals are obvious. Most beamhouse effluents are characterised by high oxygen demand, suspended and dissolved solids, sulphide, nitrogen chloride and sulphate.
Effluent treatment plants also produce high volumes of sludge, while less than a quarter of raw hides are converted into leather. The majority of solid waste is produced in the beamhouse. Thus, for today’s tanners, the chief aim is to produce high-quality leather while reducing these effluent loads – in turn, mitigating their carbon footprint.
“I think more and more tanners are becoming more environmentally minded,” says David Sabate, Stahl’s beamhouse global technical manager. “This is especially the case when it comes to the beamhouse process and effluents. It is really important for them to be aware of the latest technologies that can help them to reduce contamination in the beamhouse.”
Introducing the product
In response to the growing environmental needs of tanners, leather chemicals manufacturer Stahl has in recent years sought to adapt and expand its beamhouse portfolio. At this year’s All China Leather Exhibition (ACLE) in Shanghai, the group hosted a seminar on its work in this area.
“We are dedicated to 100% sustainable chemicals,” Joan-Carles Castell, Stahl’s global marketing manager for beamhouse operations and Proviera, told delegates.
“This is based on natural bio-reaction – meaning low carbon footprint – and renewable, biodegradable resources.”
The Dutch group is currently preparing to launch a new portfolio. Known as Stahl BeTan, it promises to offer “easy-to-adapt, responsible technologies for every step of the beamhouse and tanning process”.
Forming part of Stahl’s ‘responsible chemistry’ approach, the portfolio aims to help tanners reduce their water consumption, while driving efficiency in the beamhouse.
The portfolio includes the following products: Basozym; Basyntan; Bemanol; Decaltal; Dekalon; Eusapon; Feliderm; Imprapell; Mollescal; Proviera – Probiotics for Leather; Relugan, Sortassist, Stahl EasyWhite Tan; Stahl EasyBlue Tan; Synektan; Tanfix and Tergolix.
“With our world facing defining environmental challenges, it is increasingly important to drive sustainability in the production of high-quality leather,” said Stahl chief executive Huub van Beijeren.
“Thanks to the unique, easy-to-apply technologies within our Stahl BeTan portfolio, we are supporting tanners to lower the impact of their operations at every step of the leather-making process, as well as drive the quality of their final products. In this way, more than ever, we are delivering on our commitment to responsible chemistry.”
Clean bill of health
Several of the products within the new portfolio are already well acclaimed, such as Proviera –Probiotics for Leather, a 100% biodegradable solution used to replace conventional soaking, liming and degreasing agents, while improving the quality of beamhouse waste water.
Huub van Beijeren, Stahl
In September, Proviera – Probiotics for Leather was clean-labelled by public health and safety body NSF. The certification of ProSoak, ProSpread and ProDegreaze – the three products belonging to the Proviera stable – allows food and beverage processors that use by-products of these solutions to meet a range of certifications, including the Global Food Safety Initiative and the Hazard Analysis and Critical Control Point.
“Hide by-products are typically used for other purposes, like the production of gelatine, and so end up in the food we eat as, for example, gummy bears, butter, whipping cream and even medicine capsules,” said Marcus Breulmann, technical manager at Stahl.
“It is a foodstuff that can’t be replaced. For this reason, the raw materials used to make gelatin are clean-labelled to indicate that they are safe to use in the food and beverage industry. We are proud Proviera passed the toxicology assessment and received NSF registration as it means that, besides sustainability, we can offer even more benefits to tanners, and food and beverage processors.”
Elsewhere, Bemanol is widely recognised as one of the best solutions on the market for reducing sulphide and nitrogen levels in the effluent, and includes a concentrated biodegradable non-ionic and nonylphenol-free detergent for use throughout the beamhouse process.
Another strong declaration of intent to get ahead upstream came in 2017 when Stahl acquired BASF’s leather chemicals business – which included a wide selection of beamhouse products.
Returning to the new range, Stahl BeTan, Sabate tells Leather International that it addresses everything, from soaking and liming to deliming and bating.
“It covers every stage,” he says. “At the same time, this selection of products can help solve a number of problems, from wrinkles to stains. I would definitely say the end market is much more exacting about these things, too; they are looking for much cleaner, better leather processes.”
Improved environmental performance
As well as helping to reduce water consumption, sulphides, solids and salt, the portfolio’s other environmental benefits include lower chemical oxygen demand (COD) and biological oxygen demand (BOD). These are all areas in which tanners are looking to improve their performance, says Barcelona-based Sabate.
“From Europe and the US, to India, Pakistan and Bangladesh, all of our customers are looking to improve,” he says.
“Of course, experience around treating effluents is more advanced in some countries than others, but even in Europe tanneries still really need to reduce their quantities of sulphides, COD and BOD.”
According to Sabate – who belongs to a team headed by Claus Reineking, Stahl’s global technical manager – the new portfolio will be officially launched “sometime between now and February 2020”.
Stahl is betting on Stahl BeTan to help further differentiate the company from its leather chemicals peers when it comes to alternative, sustainable beamhouse and tanning solutions. Or as Reineking puts it, “a one-stop-shop for responsible beamhouse and tanning solutions”.
“Over the past 20 years, I would say that the beamhouse has been an area overlooked by a number of chemicals companies because of the price associated with it,” says Sabate. “So everyone has been looking to develop more economic products – especially in China – but not necessarily eco-friendly products.
“In my opinion, people lost their way focusing too much on price. Of course, you can still get low prices, but customers tend to be looking for something better. They don’t need to compromise on quality.”