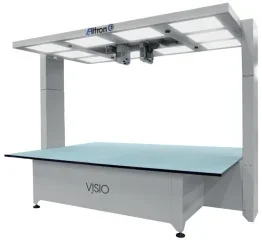
The employment website Indeed describes ‘best practices’ as “sets of methods and techniques” that produce optimal results and increase efficiency. As such, best practices cannot be immutable, and should adapt to a changing world. As Indeed continues: “Best practices can transform over time within a business or industry when new technology or ideas surface.”
We live in an era where both new technology, in the shape of artificial intelligence, and a ‘big idea’ – sustainability – are impacting how the leather sector operates now and will operate in the future.
Artificial intelligence
Sambit Bhattacharya is vice president global marketing at Rajda Industries & Exports, a manufacturer and exporter of leather products. In a LinkedIn blog post he says that in leather manufacturing, AI and machine learning, the latter being a subfield of AI, can be used to optimise processes and machine performance by analysing data from various sources, such as machine sensors and production records. AI, he adds, can “detect patterns and anomalies in data, enabling better decisionmaking and optimisation of the production process”.
Specifically, Bhattacharya points to machine learning improving the accuracy of quality control by analysing data from product inspections and identifying patterns of defects, while algorithms can optimise processes such as leather cutting and stitching, by identifying patterns of optimal performance.
AI can also enhance the maintenance of leather manufacturing equipment – by analysing data, says Bhattacharya, these technologies can predict when equipment is likely to fail, enabling preventative action to take place before a breakdown occurs. “This reduces downtime and maintenance costs, improving overall efficiency and productivity,” he notes.
Car manufacturer BMW is making good use of AI at its BMW Individual factory at Dingolfing, Germany, to cut leather for its M models. There, the cameras of a large scanner moves over the leather, looking for unevenness and imperfections. On the screen beside the scanner, a depiction of the surface of the leather is marked with dots, lines, coloured markings and numbers.
“We see which parts of the leather can be used and which are scrap,” says Marco Loistl, head of production and maintenance at the plant, explaining the process on the BMW M website. The screen shows interlocking patterns that are placed over the whole area in seconds by a computer. “And the programme also calculates the best positioning for the cutting parts,” says Loistl.
“Cutting leather is a bit like baking biscuits – you try to place as many cut portions as possible alongside each other so that you waste as little material as possible.”
Next door, at the cutting table a robotic arm armed with an oscillating blade tailors the separate parts of the leather. The cut and finished parts then go to the sewing room. The whole process used to be done by hand and eye. However, Loistl says it was proving to be too strenuous: “You can’t do this work very long at a stretch. That’s why we started feeding recognition software with the knowledge of our best employees.”
Developing the entire system – which includes the digital inspection and classification of the leather, along with nesting and cutting – was expensive and timeconsuming, but the results are worth it: BMW claims the process means a “significant” reduction in waste and about 15% less leather consumption, conserving resources, as well as the added sustainability benefit of lowering CO2 emissions. The number of wrongly cut or faulty pieces of leather has fallen by as much as 75%.
Elitron, which specialises in robotic cutting and automation, is similarly incorporating AI, in its case into the equipment it sells to its customers.
“We’re improving more and more the performance of the Elitron Opera – Automatic Nesting software, also with the help of [AI]. This translates in increasing efficiency of material yield and minimising waste during the production process,” says key account manager Giambattista Mele.
Sustainability
While one can make an immediately compelling business case for AI due to the efficiency gains it brings, the same cannot be necessarily said of sustainability – yes, it’s good ethically, but does it make sense financially? Is it, for example, worth adjusting your equipment acquisition best practices in order to be more sustainable?
In a report entitled Profits with Purpose: How Organising for Sustainability Can Benefit the Bottom Line, the multinational consultancy McKinsey argued that the “evidence indicates that sustainability initiatives can help to create profits and business opportunities”.
Of course, the most obvious saving is in energy costs, because lower CO2 emissions equals lower energy bills.
Since 2022, Elitron has been installing Elitron Power Management System (EPMS) technology on all its cutting systems, which, the company says, enables such equipment to support sustainable and eco-friendly leather production practices.
“[It is] engineered using a new electronic control board, entirely designed by Elitron, interfaced with an inverter, to manage a series of dedicated sensors, to optimise the operation of the vacuum motors,” explains Mele. “Compared to the traditional way of using a vacuum motor, with EPMS there are notable energy savings and noise output reduction. Energy consumption savings range between 30% and 40% compared to the traditional way of using the vacuum motor, while noise output levels are also greatly reduced, by up to 40% during processing. These are the main demands, in terms of sustainability, our customers require.”
As a manufacturer of splitting band knives, Lamebo, too, says its equipment can support eco-friendly leather production practices.
“If you ask us how our blades help to manage and minimise the waste generated in the leather production process,” begins the company, “we answer that the more precise a blade is… the less material, energy, time and cost are wasted for the customer.
“Our continuous research into new materials and investment in new technologies and production process is aimed at constantly improving blade performance.”
Lamebo continues: “A strong focus on sustainability and ESG [environmental, social and governance] issues is at the heart of our development and it will undoubtedly continue to be, trying to constantly improve ourselves and continue to invest, renew machinery and adopt innovative solutions to keep up with the times.
“That’s why,” it continues, “we constantly support all our 3,000-plus customers with technical suggestions to optimise the performance of the blades, and to use them efficiently and safely.”
Artificial intelligence and sustainability are reshaping operations and equipment, and integrating both into your business can deliver both greater efficiency and lower costs. But to succeed, companies have to be adaptable – or, to put it another way, as employment website Indeed suggests: it is important to constantly reevaluate and improve.