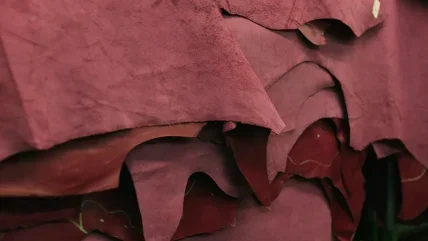
Of the many stages in the production of leather goods, the hide cutting is of prime importance, not only because it has a marked effect on the quality of the final product, but also because it has major implications for cost and efficiency. In fact, Italy’s National Association of Manufacturers of Footwear, Leathergoods and Tanning Technologies (Assomac) recently highlighted cutting as one of the key concerns for most leather manufacturers.
Not only are manufacturers putting cutting processes under the microscope, but tanneries are also coming to realise the importance of the cutting stage in optimising leather quality and reducing waste.
Indeed, a recent study by independent research organisation SINTEF and the Norwegian University of Science and Technology highlights that ‘the efficient utilisation of the leather hide has prime importance, which can be attributed to the fact that the cost of the leather hide often constitutes a significant proportion of the manufacturing costs, such that increasing its utilisation provides significant cost savings’.
‘As a result, there has been a lot of attention in the leather industry to improve the nesting algorithms for determining how to fit a variety of products onto hides’, continues the study, noting that ‘to most companies, the evaluation time and computational resources needed by these algorithms to deliver optimal results are not affordable, which often leads to the acceptance of sub-optimal results for the hide utilisation, and of results that do not suit pre-determined production plans.’
There is, therefore, much scope for innovation in many aspects of the cutting process, including nesting to optimise hide utilisation, and a drive to be more accurate when cutting leather to make the most of high-quality materials and reduce costs when producing the most valuable leather goods.
In recent years, manufacturers of cutting machines have listened to the call for innovation and have striven to build machines that deliver quicker setup, faster operation and better leather yield.
Automation for automotive
Among the manufacturers that have taken an in-depth look at how automation can vastly improve leather utilisation in the cutting process is Lectra. Its Versalis Auto leather-cutting solution has been designed to contribute to a more efficient production cycle and deliver increased yield efficiency to achieve optimised leather use and savings. Much of its value lies in precision hide analysis as well as cutting quality.
These factors enable manufacturers to handle increasing complexity while managing fluctuating production batches. Versalis also helps producers of leather for the automotive industry to reduce your time to market control costs to increase margins, and improve overall manufacturing competitiveness. Designed specifically for mass production, it handles all stages from hide digitisation to the production of cut parts, helping suppliers achieve the highest level of quality, no matter what the grade of leather, with no additional tooling costs.
“Versalis is a digital leather-cutting machine,” says Nicolas Favreau, marketing strategy director, automotive at Lectra. “Thanks to decades of Lectra expertise in leather, Versalis technology brings performance into the leather cutting room for mass production in the respect of automotive standards. The Versalis Auto leather-cutting solution contributes to a more efficient production cycle and increased yield efficiency, resulting in optimised leather use and savings.”
The latest step forward driven by Lectra’s experience in the market and its understanding of its customers’ needs, as well as an appetite for innovation, is its adoption of new technologies such as cloud computing, big data, the industrial internet of things (IoT) and advanced analytics.
“Industry 4.0 readiness is and has been at the heart of Lectra strategy for many years now,” says Favreau. “Data intelligence monitors and optimises overall leather cutting operations. Versalis is powered by automated nesting algorithms and the latest Computer Numerical Control (CNC) technologies.”
“The machine has more than 250 embedded sensors, sharing data for real-time process and cost control,” he adds. “Live reporting with personalised KPIs increases cutting room and operators’ efficiency. Being available per site, reporting would also enable comparison between several CNC productivity measures.”
Since the launch of LeatherSuite V7 in 2019, Lectra has been hard at work on refinements to its software solution, which provides enriched data for process optimisation and streamlined execution, enabling manufacturers to achieve their performance objectives and monitor production output.
“LeatherSuite version 8 increases productivity up to 10% with significant improvement steps on the threehead cutting machine,” says Favreau. “Now faster than ever –adding a new head to an existing machine and moving from two to three heads increases productivity by 15%. Also, the new version improves nesting efficiency by up to 0.5%, which translates into large annual material savings.”
This extra nesting efficiency is derived from a cluster of five embedded computers working together to improve performance. They rely on powerful algorithms to analyse multiple nesting solutions to determine the optimal use of material and reduce cutting errors.
Similarly, scanner recognition has been improved by replacing the green conveyor belt with a blue one, which provides better contrast between hides and the cutting surface. The zero-buffer performance – which leaves no space between separate cut pieces and increases the area on each hide that can be used has been further optimised using a new cutting head slotted presser foot.
“Hardware and software enhancements based on customer feedback have improved productivity by 35% of productivity and yield efficiency by 2.5%, as well as bringing more robustness and higher durability,” remarks Favreau. “And we should not forget that all our releases are compatible with our installed base since 2011, when Versalis launched on the automotive market.”
“A new pilot strategy improves cutting quality on common lines to make zero buffer between parts a reality applicable in production,” he adds. “This high degree of precision and repeatability contributes to quality standardisation, reducing the level of variability due to employee skill level or team turnover.”
Automatic advanced nesting features have increased material savings by up to 7% compared to manual processes. Maximising hide yield in this way also improves environmental sustainability by creating less waste.
“Throughput is another key KPI in the automotive market that we are taking seriously,” Favreau continues. “The algorithm and the new PC cluster addition enable the best positioning of parts on the leather hide. This new release improves nesting performance, hide-saving and also efficiency. It is widely recognised as the best automatic nesting solution on the market to guarantee the maximum yield.”
Elite systems stem from innovation
At Elitron, a leading name in computerised design and in CNC automatic cutting systems, innovation has developed a whole range of equipment. As with Lectra, the emphasis is on incremental improvement rather than a wholesale revolution in design.
“The highly precise cutting results from Elitron’s cutting systems are achieved by combining numerous factors,” explains Paolo Malatesta, Elitron’s executive director. “Firstly, the construction of the systems should be considered. All systems have been designed and built to guarantee robustness, stability and durability, and constant high quality over time. The working area of our cutting systems is made up of solid mono-block cellular steel structure, divided into individual vacuum sectors.”
“The Booster is our best-selling cutting system for the leather and fashion sector,” he adds. “Although the system has changed greatly over time, the name remains the same and is synonymous with a top-quality cut and durability. Many customers, still today, have some of the original Booster models still in their production facility.”
The Booster comes with either five or seven tools, among them electric and pneumatic knife tools, standard and shaped rotary perforators, punches, and a pen module, all housed on a sturdy multi-tool carriage designed for fast tool changeover.
10%
The productivity increase caused by LeatherSuite version 8.
Lectra
35%
The productivity increase caused by hardware and software enhancements based on customer feedback.
Lectra
“With the introduction of printed leather, Elitron developed a camera and software system to accurately match the cutting path with the printed images,” continues Malatesta. “The proprietary Seeker System uses a camera to identify the printed reference points on materials and uses these to synchronise and manage the cutting path for extreme cutting precision, all automatically.”
“Elitron was the first to introduce this technology over ten years ago in the digital print market and continues to lead the way in camera technology for cutting systems,” he adds. “Then there is the KUDOS conveyor cutting system that has been specifically engineered to perfectly cut leather and synthetic roll materials for footwear and leather goods. Now with faster acceleration and cutting speeds, productivity can be increased by up to 40% compared to the same job being processed on previous models.”
Elitron’s latest innovation is the Visio acquisition and nesting system, which comes with its latest digital technology – the Elitron Digital Infrared (EDI).
“This infrared pen allows the operator to identify quality areas, holes, and marks on the leather hide but without marking the leather at all,” explains Malatesta. “No more having to check the screen continually. The digital, highly luminous projected marks are clearly visible and colour-coded directly on the leather. Not only does this save time but it’s also far more ergonomic and practical for the operator.”
No stopping now
Innovation is an on-going process for both Elitron and Lectra, as well as other manufacturers. Mercier Turner, for instance, has a new water jet trimming system for raw, wet blue or crust. Named Cortina, it comes with an automatic vision system and can greatly improve productivity compared to hand trimming.
“Both Elitron’s on-board nesting and assisted material collection use Augmented Reality (AR) technology for an overall ‘stressless process’,” says Elitron’s Malatesta. “No longer does the operator have to question their actions as they are guided throughout the entire process. AR is helping to create a far more interactive experience for the operator.”
“Scanner evolution and automation are in continuous development,” adds Lectra’s Favreau. “Versalis is equipped with a projector, similar to augmented reality, which eases parts offloading and improves throughput. We always strive to bring breakthrough innovations from concept to market, drawing on deep insight into customer needs and market trends.”
As new technologies such as AR find their way into the cutting process, manufacturers will put them to use, but always with the same priorities in mind – productivity, efficiency and precision.