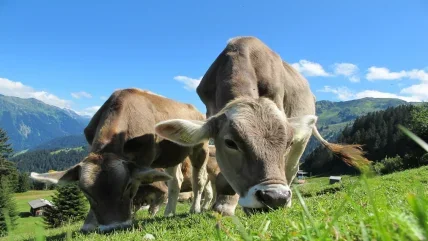
When it comes to raw materials – hides and skins – traceability is a major issue for the tanning industry. CTC has developed a simple, reliable and economically viable traceability system to ensure individual traceability (tracing each hide) from raw hide to wet-blue (or wet-white) and even finished leather.
Setting up such a system provides the leather sector with a necessary tool to improve the quality of leather and make quality charters more credible. As we can see, the traceability of leathers per se is not only a tool that, rather than creating value added directly, is a prerequisite for other actions to be meaningful. There are two main goals in implementing traceability. The first, which drove this project’s instigation, is to improve the quality of leather by being able to carry out corrective actions throughout the livestock farming chain, going back as far as the animal’s birth. The second, which emerged from the work and results obtained by the global solution designed and implemented by CTC, is to provide reliable knowledge on the origin of leathers and therefore offer guarantees in regard to suppliers by monitoring animal welfare and environmental responsibility in farming practices and slaughterhouses.
This is a 10-year project with the aim of tracing each hide or skin in a simple, reliable and economically viable way. The global solution that has been designed and developed is now being industrialised and the concept requires four different phases.
1. Make meat traceability reliably transfer to hides on the slaughter line
In ideal conditions, this solution relies on the meat traceability requirements in place in most industrialised countries. At worst, it makes hides traceable from the moment the animal is slaughtered.
The first phase of this solution is to be able to transfer a standardised and unique identification number, attributed to the animal, on to the hide (or the skin). This must take place on the slaughter line before the flaying so as to avoid breaking the traceability chain off. There are two options here: either a label is printed in real time, instantly and autonomously, when the slaughterer flashes the animal’s earring, and an operator equipped with a simple knife punches the hide on the flank to seal this label there so that it stays on the hide until the second phase of the process; or the printer is connected directly to the slaughterhouse’s computerised management system, which sends the order to print the label so that it is present with the number chosen by the slaughterhouse (slaughter number or animal identification number) at the pre-skinning labelling station at the appropriate time.
The cost of this equipment is relatively low – less than €5 per kilo – and the cost of consumables is very low as well. This first phase allows small slaughterhouses to transfer meat traceability on to hides so as to provide reliably traceable hides to their clients at an economically viable cost, and also allows large slaughterhouses to ensure the continuity of traceability between the slaughter lines and the salting workshop where hides can be marked at their core.
2. Secure the transfer of traceability from labels to the core of hides
We were quick to notice that no label or added matter on the hide could resist the beamhouse and tanning processes, which means the unit mark must be copied at the core of the material. After several trials, it was agreed that the best area for marking was on the shoulder, 15cm to the left of the back line and 15cm below the hide’s edge.
ZDHC Group
For this purpose, CTC has developed an approximately 150W CO2 laser-marking system. The time required to transfer a 14-character code to the core of the hide by marking on the grain side is about one second. This duration makes it possible to fully automate the operation and complete it in a masked time, during the process of salting or sorting raw hides. The cost of the industrial system deployed in several French slaughterhouses and tanneries ranges €100,000–150,000 depending on the level of automation and integration chosen.
At this stage of the solution’s development, the marking process has proved itself on bovine leather (ranging from calf to bull) and exotic skins (alligator and snake), and tests are under way on lamb skins. This operation can be carried out at all stages from the extraction of the hide on the slaughter line to tannery entry if the hide bears a label as previously described. Another crucial point in the success of this solution is the marked code.
This code must respect a strict typology defined in terms of size, type of marking font, and marking power by animal species and code structure (number and length of each line and information carried by each line), all of which are prerequisites to obtain very high automatic reading rates in the next phase.
3. Automatic reading of the marks from the tanning stage onwards
During the development of the previous phase, tanners received tanned hides bearing unit numbers that they had to read visually and enter in an Excel file along with mentions of any defects the hide might present. As volume increased, this operation became very tedious because the mark was affixed to the shoulder, whereas operators sort hides at the culata.
CTC was therefore commissioned to set up automatic mark-reading stations, initially located where hides are sorted at the tanned stage (wetblue and wet-white), and then at later stages of the process, up to the finished leather. For this purpose, various leather image acquisition stations were developed to suit the different configurations of sorting stations at each tannery, and algorithms based on artificial intelligence (specifically neural networks) for these stations were developed.
We could have used more common OCR-type image-processing algorithms but the results would not have met expectations. The merit of the algorithms developed is that they lie on the fact that they work like humans, that is with a very large database of marks arriving at their station.
The wet work of the tanning process is unique to each tannery, as is the provenance of leathers and, therefore, so is the acquisition station. Tannery entry processes result in distorted, masked, contrasted or hidden marks. Building a database that contains all of these eventualities and artefacts makes it possible to obtain perfectly decoded automated reading rates that exceed 90% of production. To illustrate these algorithms’ power, it should be mentioned that they can decode a number ‘3’ of which a part has been cut off because it was printed too close to a bell’s edge, if there were 3s close to bell edges in their training set. Provided it was built on a sound base, this method yields better results than human operators for deciphering marked codes.
To date, three acquisition station configurations (to capture images of the marked area) have been developed. The first acquisition station, which is the only one that is not fully automated (a human operator is required to manually scan the collar mark), allowed us to carry out the feasibility study and algorithmic modelling.
This station is composed of an area-scan camera and a portable grazing light. The operator places this station on the mark and presses a button to trigger the image capture. The system then automatically locates and rotates the mark, decodes all the characters, and stores the code in a database. The second acquisition station, which is fully automated, is designed for tanners equipped with a conveyor and an automatic stacker unit for sorting.
Each hide passes under a linear camera and a grazing light, allowing for an image of the whole hide to be reconstructed, and the algorithms then automatically search for the mark, rotate it and decode it to store the code in a database. The algorithmic processing time is about 0.5 seconds, which is considerably shorter than the time it takes to determine the potential wet-blue leather and sort it.
100%
Last year, USHSLA launched the US’s first traceability programme for hides and skins that will establish a standardised, national system of ultimately tracing all US hides and skins to the meatpacking plant or processing facility of origin. USHSLA
Our latest acquisition station, which is also fully automated, is intended for tanneries that sort hides piled on a pallet placed on a lifting table in front of the sorter. This station consists of a simple very highresolution area-scan camera and a specific light; it scans the shoulder and the entire decoding operation is carried out by artificial-intelligence algorithms that adapt to changes in image capture conditions over the course of the sorting operation. This station is currently undergoing a feasibility study. This part of the solution is CTC-patented.
4. Centralise the management system for material quality and traceability data
The last phase of the global solution we are putting forth is to set up a data management system. To this end, a common hide quality reference system has been defined in collaboration with a group of tanners and slaughterers. The aim is to collect critical information on defects occurring on tanned hides that should be passed on to the slaughterer for corrective action to be taken.
This standard describes defect categories and grades, their severity according to their number and location. This data is then fed into a touchscreen software by the sorter during the hide check, while the hide’s tracking number is automatically entered next to it in the database by the aforementioned scanning device.
The next step is the definition of a database at the output of the automatic reading to associate the tracking number with the presence of defects noted by the sorter via a touchscreen application. All this information is forwarded to the slaughterhouse for corrective actions to be carried out in the relevant farms.
It is easy to conceive of a database organised by the tanner and slaughterer relation. In this case, each tanner has any number of databases working in parallel, each of which is linked to a slaughterer or supplier. This allows tanners to centralise all the data internally on a single database, aggregating these databases and is then able to capitalise on it by extracting and analysing it. Each slaughterer can also have a centralised internal database aggregating the data coming from its tanners. Separating the system’s data into secure external databases containing only one tanner or slaughterer’s data maximises confidentiality. Building on this architecture of quality data on the raw material associated with a unitary and complete traceability goes back to each animal’s birth. The implementation of a quality charter can ensure the origin of the raw materials and guarantee animal welfare.
Behind the project
This project, conducted by CTC at the request of the French leather industry, has provided the trade with various industrial tools to ensure reliable, simple and economically viable traceability. These tools are undeniably a necessary support for the implementation of corrective actions aimed at improving hide quality and quality charters, allowing hide supply sources to be guaranteed and secured. The implementation of this solution outside France is now possible in order to provide all players with a reliable and secure technology for the traceability of raw materials, which is a crucial issue for our industries. This technology can also be applied to exotic hides in order to be able to transfer the CITES ring code to the core material, which will make it possible to remove this ring and work on the whole hide in through-feed machines.