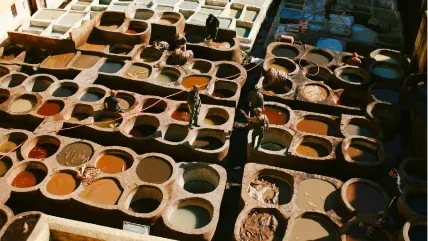
Ditching leather on sustainability grounds has become something of a trend among major brands, the latest being Volvo, which has taken what it describes as an ethical stand for animal welfare in its fully electric cars. All new fully electric Volvo models will be completely leather-free, and the company’s goal is to have 25% of the material in its new cars to be recycled and bio-based.
It will instead use, for instance, textiles created from recycled material such as PET bottles, bio-attributed material from sustainable forests in Sweden and Finland, and corks recycled from the wine industry.
The Leather and Hide Council of America was quick to respond to this move, with president Stephen Sothmann stating that it “categorically rejects Swedish carmaker Volvo’s recent announcement that by removing leather from its future electric vehicles it will somehow impact cattle and beef production globally,” adding that “hides and skins are an inevitable by-product of meat and dairy production, and if not recycled for leather, will simply be discarded in a landfill or incinerated. Volvo’s announcement will only lead to more unnecessary waste”.
Therein lies the central message about sustainability in the leather industry. Leather is made from a by-product and is a potentially circular material from a natural source that can go back into the ground – a constantly renewable raw material from the farming industry. Even if that truth is accepted, however, the processes of leather production still come under scrutiny.
“The industry realises that it must demonstrate what it is doing in sustainability to stem the rise of alternatives,” says Deborah Taylor, managing director of the Sustainable Leather Foundation. “Many tanners are making great efforts and are being held to account by certification processes. Plastic or ‘vegan’ alternatives are not held to account in the same way.”
“Vegan just means plastic and it does not have the same durability, performance and adaptability as leather,” she adds. “Water, chemicals and energy go into leather production and we need to be accountable for that and for the treatment of the end product, which can be compostable or biodegradable depending on how it is finished.”
The chemical processes used in tanning are frequently a target for critics of the industry, though much progress has been made in recent years in terms of standards, certification, product innovation and collaboration. One example is the Zero Discharge of Hazardous Chemicals (ZDHC) Programme, which is working towards the elimination of hazardous chemicals in the textile and footwear value chain.
“Leather could be a circular product, though the industry has lost track of that in recent years and is not getting that message across to the end consumer,” says Hans van Haarst, CEO of leather chemicals manufacturer Smit & Zoon. “Everything is there to make the leather value chain circular – all the technologies exist, but they are not being implemented.”
Chrome offenders
In the development of tanning chemicals, much of the focus is on removing chrome from the process. Chrome-tanned leather accounts for around 85% of leather production, having been developed as a faster, cheaper alternative to vegetable tanning. It comes, however, with the threat of environmental damage as the metal is introduced into the ecosystem. As a result, there has been a move back towards a plant-based approach to replace chrome tanning.
“In an age of depletion of natural resources and excessive use of hazardous chemicals, the leather industry presently experiences a growing market demand to adopt tanning technologies that exhibit a low environmental and human impact,” says Alessandra Taccon, project director for Ecotan at Silvateam, a producer of plant-based extracts for leather tanning. “Sustainability is life or death for the leather industry. Nowadays, consumers rank sustainability as a main priority when choosing their preferred leather goods and stand only with brands and producers who commit to nature through facts.”
“The development of more eco-friendly chemicals for the tanning process is becoming a top priority,” she adds. “There is a sense of urgency behind the quest for harmless and healthy ingredients used in tanning, which embodies a growing overall expectation of safety and health protection. When we devised Ecotan, we raised the bar to match the criteria of best-in- class existing technologies, among them chrome tanning, and took the challenge a step further by using sustainable materials that start and end with nature without causing any problems for our future.”
Ecotan is Silvateam’s flagship plant-based tanning chemical, using extracts such as chestnut, quebracho, tara, gambier and myrobalan, as well as synthetic tannins, special extracts, oils and fatliquors, tanning auxiliaries, resins and beamhouse chemicals to create products for vegetable tanning, wet-white and wet-blue tanning.
The company’s goal has been to use tannins-based technology inspired by nature to replicate the characteristics of chrome-tanned leather in terms of resistance, softness and durability. Ecotan can be used in a traditional chrome tannery to create articles that are directly comparable with or better than the outcomes achieved through traditional production.
Similarly, chemical producer Stahl has developed the Neo portfolio for both wet-end and leather finish products, which meets and exceeds ZDHC compliance criteria.
“Chemicals are a key priority and that is what we are doing, but before we do that we have to measure the environmental impact of our chemicals,” says Michael Costello, Stahl’s group director for ESG. “We have been working on lower-impact chemicals for many years and now life-cycle assessment can measure the impact to see what is making a difference.”
“That is a strong focus for us, as well as developing solutions,” he adds. “It allows us to make better decisions. We always need to check, for example, that we are not sourcing from unethical sources. Lots of people are working on it to get data that we can give to customers, so they can measure their impact. And that the chain of custody is transparent and can be certified.”
For Smit & Zoon, Nera is its disruptive portfolio of solutions. Its core product is the zeolite-based tanning agent Zeology, which is chrome-free, heavy metal-free and aldehyde-free, but does not compromise on leather performance.
“The idea existed in the 1970s and the concept was proven, but the properties of the final article were not good enough, so it disappeared,” says van Haarst. “A patented zeolite was later developed but entering into the leather market was not so easy for the company holding those patents. Basically, we broke down the product and built it back up with knowledge of how a tannery works and what it needs to be successful to apply it. One year ago, we introduced Zeology as a product as a serious competitor to chrome tanning.”
“At minimum, it provides the same performance as traditional methods,” he adds. “People want the leather to be exactly the same and to meet economic criteria, be safe to use in [tanneries], improve wastewater quality and more. The product works across all raw materials, you can make anything with it from shoes leather to automotive interiors, garments, waterproof leather. It works for all segments and all raw materials, and it is robust. A chrome-tanned shoe will be in the garbage for 300 years, but a shoe made with our product is biodegradable.”
Communication is king
Product innovation is clearly not limiting the industry’s progress towards greener tanning processes. Momentum is building behind the adoption of plant-based chemicals, though there is a long way still to go.
“There has been dramatic change in recent years,” says Costello. “In our company, sustainability has gone from being an important activity to being at the centre of the company. It is centre stage for senior management rather than on the fringe. Chemical compliance is still a huge activity – ZDHC has become a standard – and the focus is now on the impact of our products on climate change and other sustainable issues.”
“In practice, we see more tanneries using plant-based formulations such as Ecotan made with tannins and sustainable biopolymers, to replace traditional chemicals,” agrees Taccon. “We also perceive more attention to the carbon footprint of products and their sustainability metrics. Plant-based products have a double effect – we use renewable sources and do good for human beings and the planet. These plant-based materials can be used in food and wine, and are completely harmless – actually good for one’s health. That’s the way you avoid public concerns and the way you create a new friendly image for leather.”
Producers of tanning chemicals are not shying away from the scale of the task that still remains. Currently, the chemicals industry as a whole generates around 7% of anthropogenic greenhouse gases, and that proportion will increase as the energy industry decarbonises. The industry, of which the leather sector is a small part, still needs to step up, but the will is there to do that.
“It is like changing from gasoline to electric cars,” says Costello. “The infrastructure has been built around gasoline, so a lot of change is needed in infrastructure and in the supply chain – that takes time.”
“Our efforts are not yet being recognised by the end consumer,” adds van Haarst. “But a lot of work is going on through the leather value chain. There will be no progress unless the end user realises it. Brands need to change attitudes and influence the buying behaviour of the end consumer.”
When it comes to chemicals, innovation is only part of the solution. What is needed now is communication of the industry’s achievements.