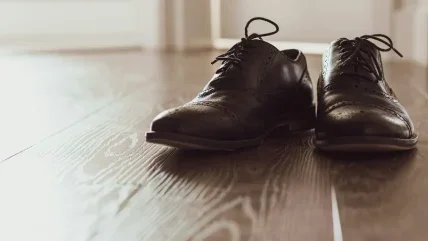
During APLF Dubai’s footwear forum, a presentation on how the Middle East can become a footwear manufacturing hub drew attention. While the talk focused on 3-D printing and biomanufacturing, it raised the question, what about leather? This was posed to one of the presenters, Nicoline van Enter, the founder of Footwearology and co-founder of the New Fashion Factory (NEFFA).
“I would prefer that the next-gen materials not present themselves as leather replacements because I don’t think they are, I don’t think they need to be,” van Enter says. Instead, she offers the suggestion that they could work in cooperation with leather, replacing ubiquitous polyurethane materials and coatings. Previously at the 2018 Shanghai Shake-up Program during ACLE, van Enter proposed using a hybrid of leather and alternative materials was the future. Since then, the possibilities for a unique alliance have grown.
Changing the mix
One of the big issues for footwear is the current mix of materials and adhesives used in today’s shoes limits longevity and recycling possibilities. But what if biotechnology could have a role in innovating the leather industry?
“Leather is a super sustainable material because of its longevity… we could create shoes with leather in constructions that last longer,” van Enter argues. When we look at end-of-life for leather, you find options such as leather recycling, but this requires grinding up the leather and adding a binder. During this process, the unique features of leather – such as breathability – are lost, van Enter says.
“Leather is a super sustainable material because of its longevity… we could create shoes with leather in constructions that last longer.”
Nicoline van Enter
This is where innovation could create new opportunities for leather, particularly in optimising the longevity of leather. As van Enter puts it: “Can we not use some of the new alternative material technologies, such as those derived from collagen, to create new binders that can fuse pieces of leather together and create a new skin?”
Van Enter also believes that another benefit would come at the product’s end-of-life, where the materials could be retrieved with the help of lab-grown leather alternatives – describing it as though it’s a rebirth of sorts.
Offcuts could be given a new purpose through using biotechnology to bind them back into skins. Or perhaps biotechnology could be used to put a grain back onto split leather, van Enter muses.
New opportunities
All of this is uncharted territory. No one has clear answers on what could be possible or what makes sense to do. What is clear, however, is there needs to be joint research and development to explore new options.
Ultimately, leather innovation will depend on the ability to adopt real out-of-the-box thinking. The industry has produced leather in the same way for centuries. There has been some incorporation of new technologies along the way, but the basic process has remained essentially the same. But could there be a new way?
There may be ways to use new materials to expand opportunities for real leather or new techniques to use raw hides, such as a collagen-based glue, that could be used to fuse leather pieces together.
Plant-based coatings for leather are another area ripe for innovation, according to van Enter. “Today’s leather coatings are plastic –PU– and what we really need are good plant-based coatings.”
It is also possible to envision using lab-grown plantbased materials to repair blemishes and scars in natural hides. This could minimise or even eliminate hides that have bites, scratches or marks going to waste.
Alternative materials, such as those grown from mycelium, still need to be tanned. This also presents another opportunity for the leather industry. In fact, an article discussing alternative materials in the September 2022 issue of Leather International noted this fact. The preference for developers of such materials would be to work with tanners who already have great expertise, but they could go it alone if tanners balk.
Some traditional tanners are already on board. ISA TanTec has its own division called Creation of Sustainable Materials (COSM) and Germany’s Helle- Leder has teamed up with Bolt Threads, which developed the mycelium-based material Mylo.
Footwear
To date, alternative materials have mostly been used to produce bags, garments and upholstery. But these new materials face a tough road when it comes to replacing leather in footwear. They must meet leather specifications for shoes that are more stringent than plastic or textiles. So far, several brand groups have said properties like tear and tensile strength or abrasion are not good enough yet.
One of van Enter’s ventures, NEFFA, is billed as “the only 3D manufacturing method allowing for seamless and custom products grown from
“Let’s be smart and see how we can use materials in a smart way. We already have lots of leather, so we are responsible for finding a use for that leather.”
Felipe Fiallo
home compostable mushroom roots and other biomaterials”. Essentially the innovation is growing a shoe. By eliminating most of the manual labour, all the cutting and stitching, it takes automation to an entirely new level. These biomaterials are not just leather replacements but are intended to be materials in their own right, since they can do things that leather can’t.
It’s well-understood that as footwear production moves toward ever-greater automation, leather is at a disadvantage. Leather can be difficult to work with precisely because it is a natural material with inherent inconsistencies. Van Enter goes on to explain that leather also requires cutting and sewing, a segment of footwear production that is increasingly under pressure due to labour costs and availability. So far, this is where much of the innovation in footwear has been focused.
But this doesn’t mean there’s no room for innovation when using leather in automated production technologies. “Vacuum forming and wet-moulding leather can work really well when it comes to forming a shoe in one go,” van Enter says. She adds that, while it’s not a common method, it is possible and minimises stitching and labour.
Design first
Of course, designers will have to get on board with new innovations in materials to make change happen.
Felipe Fiallo is already laying the groundwork for entirely new footwear concepts, many of which incorporate leather. The Milan-based sustainable footwear and senior industrial designer combines the worlds of biology, leather and technology to create innovative footwear designs. Like van Enter, Fiallo enjoys exploring ways to challenge technology and thinking differently to transform materials into performative objects – in this case, shoes.
“Let’s be smart and see how we can use materials in a smart way. We already have lots of leather, so we are responsible for finding a use for that leather,” he explains. Fiallo has developed and patented a process for the thermal transformation of leather for use in footwear, where in one fell swoop a single piece of leather is formed into a shoe.
His talent for innovation should not come at a surprise, given he won the ITS Fondazione Ferragamo Award in 2020. His brand received the MICA Emerging Designers award in 2022, the same year he launched his first eco-futuristic collection at MICAM Milano.
Fiallo has also created a shoe that combines two natural materials, vegetable-tanned leather with an algae-based plastic. The resulting footwear can last for 18 months to two years – the average length of time a person keeps a pair of shoes – and once used, the shoes can become fish food. Customers can toss them into the ocean without worry because they aren’t toxic and fish happily eat the components. Meanwhile, leather meal can already be used as fish food or as a supplemental protein source for livestock, and the leather elements can be separated from the algae-based plastic since there is no glue used, only stitching.
Fiallo points out that materials are only about 20% of the problem in footwear manufacturing. “It’s about the fashion system itself. 90% of the issues in footwear production should be solved in the process of design, not in the process of making,” he says.
“The future isn’t about sustainability because we’re not sustainable as we are. It’s about originality. We have to match technology with tradition where technology is not the goal. It’s the bridge to arriving at new products and new solutions.”
Global mycelium leather market
The Covid-19 pandemic significantly impacted the global mycelium leather market, with the market estimated to be valued at $24.07m in 2022.
However, the market is projected to experience significant growth, reaching a revised size of $226.81m by 2028 and a CAGR of 45.33% for the forecast period of 2022–28.
With the economic changes brought about by the pandemic, in 2021 the dyed mycelium leather segment accounted for 56.72% of the global market. But it has a projected value of $120.25m by 2028, growing at a revised 43.98% CAGR from 2022–28.
Additionally, the footwear segment is expected to grow at a CAGR of 43.66% throughout the forecast period.
In 2021, the North America mycelium leather market size was $5.02m, while Europe was $6.76m. The proportion of the North American market was 38.53% in 2021, while Europe’s market share was 51.88%.
It is predicted Europe’s market share will increase to 53.28% by 2028. The major global manufacturers of mycelium leather include MycoWorks, Bolt Threads, Ecovative and ISA Industrial, among others. In terms of revenue, the top three players held a 95.47% market share of mycelium leather in 2021.